How Product Lifecycle Management and Supply Chain Management has come close to give a new spark to business
Published on 02 August, 2015
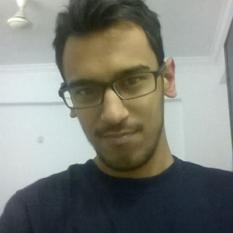
Design Engineer at
Tata Consultancy Services
The quest for faster product development, better
resource utilization and stronger market presence is not new to the
manufacturing industries. A last few decades have witnessed accelerated
technological improvements irrespective of the field of application. Right from
the post-World War II era the enterprises have been evolving in new ways to
increase efficiency in all the processes including manufacturing operations and
sales. With new strategic developments like introduction of product lifecycle
management (PLM) and an established supply chain management (SCM), the
organizations have witnessed a whole new horizon of performance. Now when we
are well into the digital age, the enterprises are not hesitating to exploit
its benefits to boost their revenues. It started with computer aided designing
and now the world is looking towards a complete digital enterprise where all
the major processes are being carried out through software, may it PLM, SCM,
customer relationship management (CRM) or the whole enterprise resource planning
(ERP). Digitalization has also developed a platform where collaboration of
different pillars of an enterprise can be more simplified and put to practical
application in the best possible way.
It has been seen that automotive and high-tech electronics companies have in some way or the other collaborated their PLM and SCM locally and globally to revive their presence by making products not just with higher value but also suitable for the needs of the different consumers and setting new benchmarks in the associated timelines of product introduction. Now other enterprises are following the same mantra and making it work every time successfully. PLM was introduced with a vision to make enterprises more responsive to the changing market trends and meeting customer expectations. It helped companies reduce product development time and time to market. As the complexity of the functioning of manufacturing giants increased as a result of involvement of more number of suppliers and more technically advanced products, PLM played a major role in maintaining the right harmonics to yield best results. SCM came as a tool to enhance the capability of the enterprise to put right product in front of the right customers at the right time to maximize the benefits. Though it has existed for a long time but a proper structure gained importance when the demand became more diverse and affected by demographic and geographic factors. The new trends now focuses on how effectively both can be merged together to reap the best results and make them work seamlessly towards the common goal.
Why the closeness is needed? The scenario of product development has changed in this era as concurrent engineering has taken over the engineering workflow. Now the suppliers are being made ready to provide raw materials and the production engineer starts finalizing the design of tools and dies even when the final design is not ready. More and more processes are being outsourced, more suppliers are being involved in the pre-production phases and more specific products are being introduced for the demands of different geographies. Managing the agile product lifecycle without a strong supply chain network has become impossible. For removing the inefficiencies within the system a lot of processes from both PLM and SCM are being fused together and the presence of digital platforms has made this fusion perform better. The software players are today offering products with features consolidated from both PLM and SCM as this interrelation had been envisaged quite before. Now let’s go through the important factors that have paved the way for such interrelation.
§ New strategy and structure of the enterprise: It has become common for the manufacturing giants to establish their designing and manufacturing facilities at different location across the globe as a part of the new strategy. Not only more number of suppliers is being added at different tiers but also their involvement in product design and delivery has been increased. This has increased the efficiency of the companies and at the same time increased the complexity of the process. To ensure proper visibility across the workflow digitalization of the processes have become unavoidable. Instead of offering a platform to be used just within the core enterprise to manage workflows, different PLM software today are offering solutions to connect the suppliers also to realize the correct effectiveness fully . SCM offerings are also getting aligned to achieve the common goal of removing the inefficiencies. The suppliers, core enterprise and the retailers are coordinating closely to help products reach customer in time. The fine boundaries between segmented PLM and SCM are being diffused to channelize all available resources towards realizing a perfect end to end flow of goods and information. In the time when a manufacturing giant designs a product In the US in coordination with offshore development centers in India, manufactures and assembles in China and sells all over the globe, the complete merger of the various supply chains throughout the lifecycle of the product is what being demonstrated.
§ Global Presence: The companies are never founded to offer products and services just locally. They always thrive to expand and go global. To achieve global presence they have to meet different demands in different economies following different taxation rules solving different logistic problems and different compliance issues etc. All these issues combines with all the different product they offer to make it a big challenge to overcome both in product lifecycle and the supply chains. The demand for different products which meet all the local issues in different part of the world has left no other option than involving the supply chains fully into product development. The companies now customize all their product development workflow with the locally established supply chains to meet customer demand in different areas. This also calls for better integration of the supply base along with a need of building more intense and inclusive relationships with suppliers where more design and manufacturing plans are shared. Also involving suppliers and vendors in different PLM phases help them make the product more aligned with customer demands even when the CRM is not either established or fully functional.
§ Building Resilience: Organizations today are giving more attention towards building a workflow which has the immunity to fluctuating demand, uncertain economic conditions, ever growing competition and even physical and infrastructural damages. To develop and place products according to quick changing trends over different markets is the key to sustain a continuous growth. It has been seen that even giving read only access of digitalized PLM platforms to the suppliers has helped in keeping them updated about the new design changes being planned and reducing the time taken by them to be ready to implement those changes in the new batches of the products being rolled out. Moreover thorough integration of PLM and SCM can make key manufacturing aspects of Just in Time (JIT) become easy to adapt over the whole process and can align the timelines of different suppliers and retailers with the core enterprise.
Why it was so obvious?
The concepts and structure of product lifecycle management and supply chain management are well established now. Software platforms have brought PLM and SCM to new horizons where they are working on fully optimized levels. But the scenario seemed to be stagnated and saturated with the individual best efforts of the two. To further improvise the performance, the need to collaborate two important division of an enterprise was the obvious solution. This situation finally gives the obvious option of starting the integration of the two most important and well established pillars of the enterprise, those being PLM and SCM. It is a step closer to an all functional group integrated, extended ERP which is the necessity before we move into the ‘Industrial Internet of Things’ world.
Enterprises have also recognized the fact that the size of the suppliers have increased , not only in volume of production but also in number of core enterprises they work with and the number of intellectual property rights they share with those companies. The suppliers and retailers today have sometimes more experience than the core companies in specific fields owing to their exposure of working with different client and hence companies are seeking inclusive participation from those elements of the supply chain and breaking the barriers to accelerate growth. The availability of numerous offerings by software vendors both in PLM and SCM has also enabled the enterprises to have a better visibility over the whole process of PLM and SCM. The PLM software vendors are offering different solutions which include control over the amount of data shared by the core enterprises with the suppliers and retailers. Similarly introduction of RFID and barcode enabled supply chain tracking have gained relevance as it can be integrated easily with the regular SCM software offerings. Furthermore the core enterprise today is including suppliers in their key processes, sharing risks and rewards and making them partners in their profit and loss which is being possible by making PLM and SCM work closely. The companies are not just focusing solely on their vertical growth but also extending the growth horizontally among suppliers and retailers by making all the actual participant in growth perform better and thrive for success with the same spirit as the core enterprise. These factors together are fueling the growing inter relation which will not just stop here but change the whole perspective of building a digital enterprise as organizations will invest more as they will try to harness more profit out of this revolution and get high returns on their investments.
Whats is next thing we are looking at ?
The extended enterprise resource planning which will break the functional silos and remove the boundaries to mold it into one system which will give complete end to end visibility of the whole process. Moreover building the whole system into cloud will help in collecting smart data and utilizing it for increasing the productivity. It will help build a system where an end customer picking up a product from a retailer will decide the quality, quantity and time of procurement of the raw material at some tier 2 or 3 supplier. A leading retail chain has made its customer and supplier data collected for over 2 years online, to increase its sales.
This unified all functional division integrated extended enterprise will actually make the organization ready for industry 4.0 and Industrial internet of things era. The growing interrelation is not just an option but a compulsory pre-requisite for stepping fully into new world of connected devices and products. Actually the enterprise which can establish this kind of infrastructure stands a chance to rise above all market competitions and set benchmarks which will be absolute as the best available combination of resources available on globe will be used through big data analytics running over the completely consolidated ERP. The famous Just-in-Time will step down to make way for Just-in-Real-Time. So organizations should start considering putting all its process into one single digital platform to get maximum returns for every dollar they invest.
Images have been used from Gartner reports and google images.
It has been seen that automotive and high-tech electronics companies have in some way or the other collaborated their PLM and SCM locally and globally to revive their presence by making products not just with higher value but also suitable for the needs of the different consumers and setting new benchmarks in the associated timelines of product introduction. Now other enterprises are following the same mantra and making it work every time successfully. PLM was introduced with a vision to make enterprises more responsive to the changing market trends and meeting customer expectations. It helped companies reduce product development time and time to market. As the complexity of the functioning of manufacturing giants increased as a result of involvement of more number of suppliers and more technically advanced products, PLM played a major role in maintaining the right harmonics to yield best results. SCM came as a tool to enhance the capability of the enterprise to put right product in front of the right customers at the right time to maximize the benefits. Though it has existed for a long time but a proper structure gained importance when the demand became more diverse and affected by demographic and geographic factors. The new trends now focuses on how effectively both can be merged together to reap the best results and make them work seamlessly towards the common goal.
Why the closeness is needed? The scenario of product development has changed in this era as concurrent engineering has taken over the engineering workflow. Now the suppliers are being made ready to provide raw materials and the production engineer starts finalizing the design of tools and dies even when the final design is not ready. More and more processes are being outsourced, more suppliers are being involved in the pre-production phases and more specific products are being introduced for the demands of different geographies. Managing the agile product lifecycle without a strong supply chain network has become impossible. For removing the inefficiencies within the system a lot of processes from both PLM and SCM are being fused together and the presence of digital platforms has made this fusion perform better. The software players are today offering products with features consolidated from both PLM and SCM as this interrelation had been envisaged quite before. Now let’s go through the important factors that have paved the way for such interrelation.
§ New strategy and structure of the enterprise: It has become common for the manufacturing giants to establish their designing and manufacturing facilities at different location across the globe as a part of the new strategy. Not only more number of suppliers is being added at different tiers but also their involvement in product design and delivery has been increased. This has increased the efficiency of the companies and at the same time increased the complexity of the process. To ensure proper visibility across the workflow digitalization of the processes have become unavoidable. Instead of offering a platform to be used just within the core enterprise to manage workflows, different PLM software today are offering solutions to connect the suppliers also to realize the correct effectiveness fully . SCM offerings are also getting aligned to achieve the common goal of removing the inefficiencies. The suppliers, core enterprise and the retailers are coordinating closely to help products reach customer in time. The fine boundaries between segmented PLM and SCM are being diffused to channelize all available resources towards realizing a perfect end to end flow of goods and information. In the time when a manufacturing giant designs a product In the US in coordination with offshore development centers in India, manufactures and assembles in China and sells all over the globe, the complete merger of the various supply chains throughout the lifecycle of the product is what being demonstrated.
§ Global Presence: The companies are never founded to offer products and services just locally. They always thrive to expand and go global. To achieve global presence they have to meet different demands in different economies following different taxation rules solving different logistic problems and different compliance issues etc. All these issues combines with all the different product they offer to make it a big challenge to overcome both in product lifecycle and the supply chains. The demand for different products which meet all the local issues in different part of the world has left no other option than involving the supply chains fully into product development. The companies now customize all their product development workflow with the locally established supply chains to meet customer demand in different areas. This also calls for better integration of the supply base along with a need of building more intense and inclusive relationships with suppliers where more design and manufacturing plans are shared. Also involving suppliers and vendors in different PLM phases help them make the product more aligned with customer demands even when the CRM is not either established or fully functional.
§ Building Resilience: Organizations today are giving more attention towards building a workflow which has the immunity to fluctuating demand, uncertain economic conditions, ever growing competition and even physical and infrastructural damages. To develop and place products according to quick changing trends over different markets is the key to sustain a continuous growth. It has been seen that even giving read only access of digitalized PLM platforms to the suppliers has helped in keeping them updated about the new design changes being planned and reducing the time taken by them to be ready to implement those changes in the new batches of the products being rolled out. Moreover thorough integration of PLM and SCM can make key manufacturing aspects of Just in Time (JIT) become easy to adapt over the whole process and can align the timelines of different suppliers and retailers with the core enterprise.
Why it was so obvious?
The concepts and structure of product lifecycle management and supply chain management are well established now. Software platforms have brought PLM and SCM to new horizons where they are working on fully optimized levels. But the scenario seemed to be stagnated and saturated with the individual best efforts of the two. To further improvise the performance, the need to collaborate two important division of an enterprise was the obvious solution. This situation finally gives the obvious option of starting the integration of the two most important and well established pillars of the enterprise, those being PLM and SCM. It is a step closer to an all functional group integrated, extended ERP which is the necessity before we move into the ‘Industrial Internet of Things’ world.
Enterprises have also recognized the fact that the size of the suppliers have increased , not only in volume of production but also in number of core enterprises they work with and the number of intellectual property rights they share with those companies. The suppliers and retailers today have sometimes more experience than the core companies in specific fields owing to their exposure of working with different client and hence companies are seeking inclusive participation from those elements of the supply chain and breaking the barriers to accelerate growth. The availability of numerous offerings by software vendors both in PLM and SCM has also enabled the enterprises to have a better visibility over the whole process of PLM and SCM. The PLM software vendors are offering different solutions which include control over the amount of data shared by the core enterprises with the suppliers and retailers. Similarly introduction of RFID and barcode enabled supply chain tracking have gained relevance as it can be integrated easily with the regular SCM software offerings. Furthermore the core enterprise today is including suppliers in their key processes, sharing risks and rewards and making them partners in their profit and loss which is being possible by making PLM and SCM work closely. The companies are not just focusing solely on their vertical growth but also extending the growth horizontally among suppliers and retailers by making all the actual participant in growth perform better and thrive for success with the same spirit as the core enterprise. These factors together are fueling the growing inter relation which will not just stop here but change the whole perspective of building a digital enterprise as organizations will invest more as they will try to harness more profit out of this revolution and get high returns on their investments.
Whats is next thing we are looking at ?
The extended enterprise resource planning which will break the functional silos and remove the boundaries to mold it into one system which will give complete end to end visibility of the whole process. Moreover building the whole system into cloud will help in collecting smart data and utilizing it for increasing the productivity. It will help build a system where an end customer picking up a product from a retailer will decide the quality, quantity and time of procurement of the raw material at some tier 2 or 3 supplier. A leading retail chain has made its customer and supplier data collected for over 2 years online, to increase its sales.
This unified all functional division integrated extended enterprise will actually make the organization ready for industry 4.0 and Industrial internet of things era. The growing interrelation is not just an option but a compulsory pre-requisite for stepping fully into new world of connected devices and products. Actually the enterprise which can establish this kind of infrastructure stands a chance to rise above all market competitions and set benchmarks which will be absolute as the best available combination of resources available on globe will be used through big data analytics running over the completely consolidated ERP. The famous Just-in-Time will step down to make way for Just-in-Real-Time. So organizations should start considering putting all its process into one single digital platform to get maximum returns for every dollar they invest.
Images have been used from Gartner reports and google images.